I förra inlägget beskrev jag hur vi identifierade de allvarligaste felen på tornursverket.
Denna gång handlar det mest om – gången!
Vi började med att göra iordning mellan- och gånghjulen. Har en bred polerfil för grova tappar, den planslipades och gjordes iordning för tappolering av rejälare slag. Först med diamantbryne, sedan med slippapper.
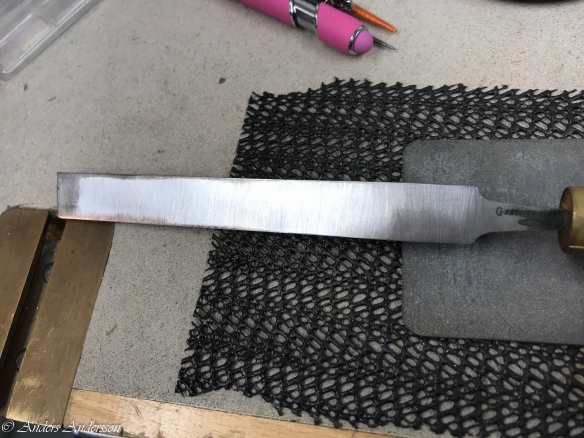
Planslipar polerfilen på ett diamantbryne först.

Skärper filen med ett 60 mic slippapper.

Mellanhjulet uppsatt i svarven för polering.

Snart snygg och fin.

Tappen polerad och fin.

Mellanhjulets driv renslipad och polerad.

Sidorna på hjulet slipas rena och behandlas med zaponlack för att skydda mässingen mot oxidation.
Vårt största bekymmer var det stora slitaget i gånghjulets driv. Hur går man tillväga för att lösa det och varför hade det uppstått?
Laga driven eller tillverka en ny?
Kollade upp vilken modul driven hade – 1,5 – Thornton i England har en drivfräs som kunde fungera.
Men vi har också en liten TIG-svets – PUK. Med hjälp av den kan man addera material, lägga på nytt material som blir ny yta i driven.
Att fräsa en så stor driv innebär flera problem för en mindre verkstad; måste köpa in lämpligt material, anskaffa en fräs, hur sätter man upp och svarvar till ämnet, hur härdar och anlöper man – många frågetecken.
Testade den senare metoden först – lägga på material med svetsen.

Djupa märken i driven.

Ett första lager av svetspunkter har lagts på. Materialet jag adderar med är blåstål. Använde blåstål i storlek 0,40 och 0,50 mm.

Slipar av topparna på svetspunkterna, sedan är det dags att fylla på ytterligare material tills ytan blir jämn och fin. Vår svets tillhör första generationen – på senare modeller kan man lägga svetspunkterna mer exakt och med ett jämnare flöde.

Driven klar, polering återstår.
När driven var klar var det tid att undersöka varför driven hade blivit så sliten. Måste testa ingreppet mellan gånghjulet och mellanhjulet – var centrumavståndet rätt?
Då sätter man upp hjulen i en ingreppscirkel – men…
Hur stora ingreppscirklar finns det?
Vår största var alldeles för liten. Vad göra?

Tillverkar ett mässingsrör.
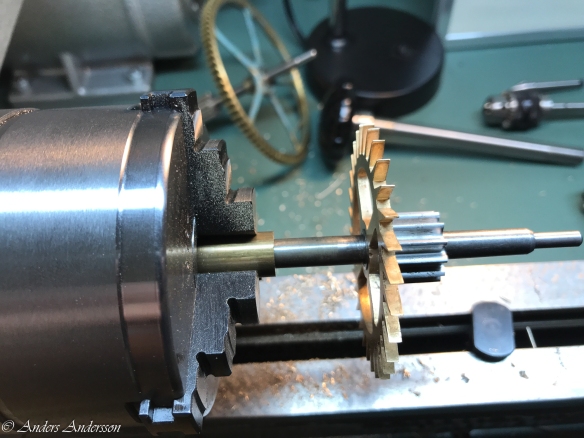
Röret anpassas för gånghjulets axel.

Röret anpassat så att gånghjulet kan snurra fritt och glappfritt.

Klämde fast röret i svarvens support och satte upp mellanhjulet med en spännhylsa i svarven. Med hjälp av veven på supporten kunde jag sedan justera centrumavståndet tills jag fick bästa möjliga ingrepp.
Hittar det bästa centrumavståndet.

Mäter avståndet mellan axlarna.

Nu har jag måttet mellan axlarna, sedan mäter jag axlarnas diameter, dividerar med två och lägger till måtten på 63,3 mm. Sedan kontrollmäter jag i själva verket och jämför avstånden.
Det visade sig att mitt uppmätta centrumavstånd och det som fanns i klockan överensstämde, så någon justering behövdes inte. Man får väl betänka att klockan fungerat sedan 1906 med allt vad det innebär av smuts och partiklar i verket. Alla föroreningar bildar en smet av slipmedel som under årens lopp äter sig in i stålet. Får hoppas att den nya ytan vi gjort kommer att hålla i 100 år till!
Dags att åtgärda haken. Plocka isär alla delar, slipa och polera paletterna.

Hakbom och pendelförare, rengöring, slipning och polering.

Haken fastsatt med insexskruv. Original?

Hakpalett uppsatt i trefoten. Några drag mot slippappret visar att ytan inte är plan.

Några tag till så är den plan och färdig för polering.

Black polish som engelsmannen säger!

Eller spegelpolering som vi säger.
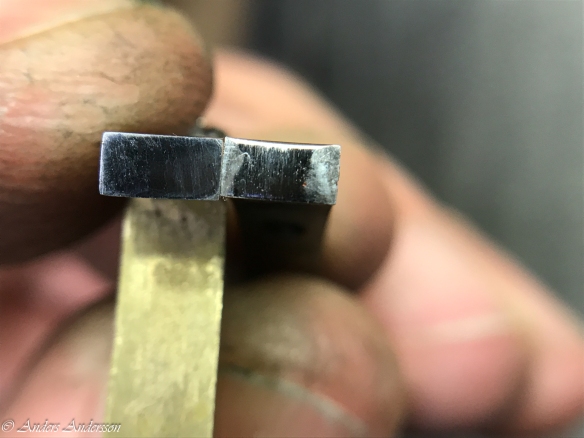
En palett polerad och klar, den andra väntar på sin tur. Notera det avrundade hörnet på den oslipade paletten.
Flera gånghjulständer var skadade och böjda. För att kunna rikta upp dem på ett bra sätt tillverkade jag en passbit som passade mellan två tänder (oskadade). Först grovriktade jag med en fin flacktång, sedan använde jag passbiten som mall. När alla tänder var riktade satte jag upp en mätklocka och kontrollerade så att alla tänder var lika långa. Det visade sig att två tänder var såpass skadade och korta att jag blev tvungen att fälla in nytt material.

Kontrollmätning.

Har märkt upp vilka tänder som behövde riktas. Slipade till en passbit som tolk och hjälp vid riktningen.
När alla tänder riktats provade jag gånghjul och hake i verket. Skulle de skadade tänderna fungera?
De visade sig att två tänder var alldeles för korta, fallet hamnade inte på vilytan utan på hävytan. Så kan man inte ha det!

Sätter upp en slitsfräs i fräsmaskinen. Tar hjälp av en USB-kamera för att rikta in fräsen.

Skär bort en del av tanden.

Spåret klart.

Löder in en mässingsbit.

En blivande ny tand.

Skär bort överflödigt material.

Nya tänder på plats.

Tandinfällningen klar.

Båda tänderna klara.
Ett första test för att se om de nya tänderna fungerar.
Test med pendel.
Det var allt för denna gång!